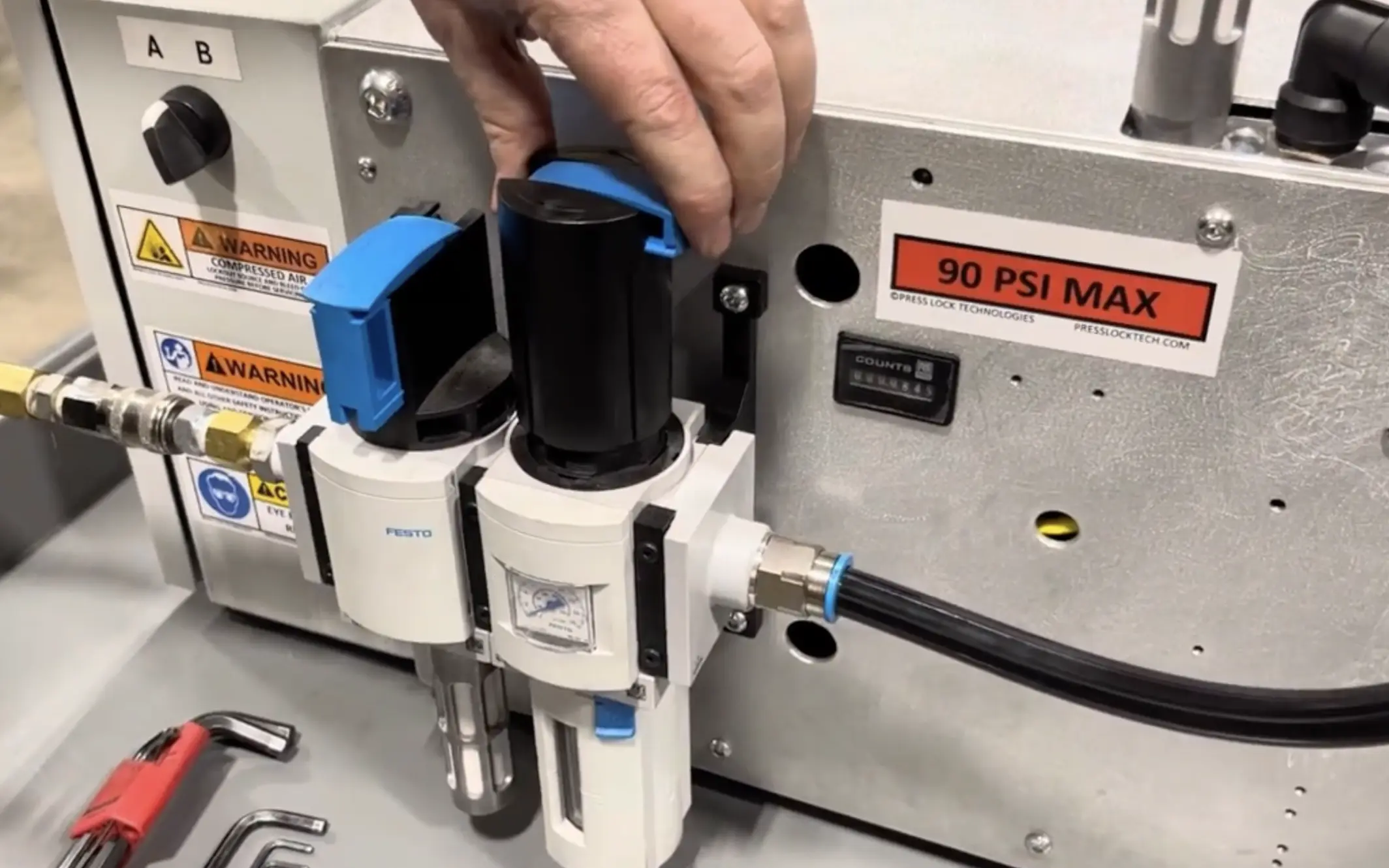
Clinching machines are essential for joining materials without the need for additional fasteners like rivets or screws.
Different technologies power these machines, each with its own benefits and drawbacks.
In this article, we’ll help you decide which type of clinching technology–pneumatic, hydraulic, servo, or mechanical–fits your needs.
The different technologies that power clinching machines
Four potential technologies power clinching machines:
- Pneumatic machines use compressed air to generate the force needed.
- Hydraulic machines use pressurized hydraulic fluid.
- Servo machines use electric servomotors to control the clinching process with high precision.
- Mechanical machines have a crankshaft that spins to generate force.
We’ll go into each technology in more depth, but these are the key differences between them:
- Pneumatic clinching machines are best for cost-effective and fast operations and are suitable for lighter applications with moderate force requirements.
- Hydraulic clinching machines are ideal for high force and precision and are suitable for heavy-duty applications and tougher materials.
- Servo clinching machines are optimal for complex and high-quality requirements, offering the highest level of precision and control.
- And hydropneumatic machines can offer the best of both pneumatic and hydraulic worlds for portable applications.
Pneumatic or air-powered clinching machines
Pneumatic clinching machines, also known as air-powered clinching machines, use compressed air to generate the necessary force.
A compressor provides compressed air, which is directed into a cylinder. The air pressure drives a piston, which moves the clinching tool. The tool presses the materials together, deforming them to create a mechanical interlock.
Pneumatic clinching machines generally have faster cycle times and are suitable for light- to medium-duty applications.
They’re relatively easy and cheap to maintain if you have someone who can troubleshoot pneumatic systems. While they can have higher energy costs and can be loud, they don’t use energy when you aren’t doing production.
We offer two pneumatic clinching machines: the T-Rex, which is floor-mounted, and Thor, which is desk-mounted.
Hydraulic clinching machines
Hydraulic clinching machines use hydraulic fluid under pressure to generate the force needed for clinching.
A hydraulic pump pressurizes the fluid, which is then directed into a cylinder. This pressurized fluid moves a piston that drives the clinching tool deforming the materials to create a joint.
Hydraulic systems can generate higher forces, making them a good choice for heavy-duty applications or for thicker and tougher materials. They’re more consistent and very reliable.
But hydraulic fluid can be messy, polluting, and highly corrosive. Dealing with oil leaks is one of the biggest disadvantages of working with a hydraulic machine. The pump is always running, whether you’re doing production or not, which makes them pretty loud.
Servo clinching machines
Servo clinching machines leverage electric servomotors to drive the clinching tool.
Electronic feedback systems control these servomotors, which manage the tool’s position, speed, and force with high precision. Real-time adjustments and monitoring ensure accurate and repeatable joints.
Servo machines are the most technologically advanced option. They’re highly precise and can repeat a joint perfectly each time. Because they’re capable of real-time adjustments and monitoring, they take a lot of the quality control burden from you. They’re also very energy efficient and quiet.
Unsurprisingly, that makes them extremely expensive. If they stop working, it’s harder to diagnose where the issue is coming from, and you typically need someone who is highly technical to repair them.
Servo clinching machines are perfect for advanced scenarios where high precision, flexibility, and quality are paramount, such as in medical device production. Their ability to integrate into Industry 4.0 environments for real-time monitoring and quality control adds significant value.
Mechanical clinching machines
Mechanical clinching machines use an electric motor to spin a flywheel. They have a crank shaft that does a full rotation every time to drive the clinching tool and join the metal.
They’re much less common than the other options, although they’re used a lot in the press industry. They tend to be quite fast and fairly simple to maintain.
Because the primary mechanism, the crank shaft, has to rotate 360°, any mistake in the material can cause damage to the tooling right away. Other machines are more forgiving. They’re also harder to integrate safety measure into and can be quite loud.
Hybrid clinching machines
The final option are hybrid machines.
Combining hydraulic and pneumatic technology into a hydro-pneumatic clinching machine is a great way to get a lot of power in a small area, which is especially useful for portable clinching machines. The driving cylinder of a pneumatic machine needs a lot more surface area to generate a comparable amount of force, whereas combining them with hydraulic reduces that need.
These machines push pressurized oil to a smaller cylinder which generates a lot of force. They enable you to get into smaller part geometry with equipment that is also smaller.
We offer two different types hydro-pneumatic clinching machines: Thor and the MooseJaw.
Need help deciding? Give us a call
If you're not sure which technology is the right fit for your application, just reach using our contact form or give us a call. We're happy to point you in the right direction, big customer or small.
Other articles you’ll find helpful
Take our 5-day course
Get an article every day for 5 days
Don’t have time to read everything now? Sign up and we’ll send you an article every day for 10 days.
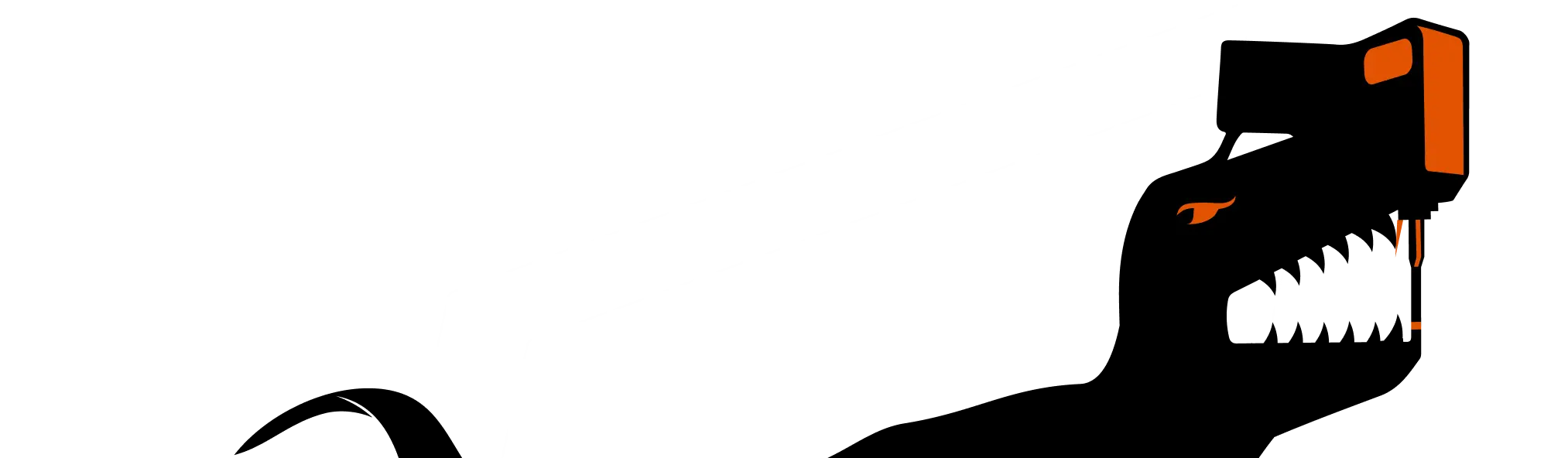