What is clinching and how does it work?
In manufacturing, clinching is a mechanical joining process used to join two or more pieces of sheet metal without the need for additional fasteners such as bolts, screws, or rivets. This process creates a strong, permanent, and reliable connection between the metal pieces.
How the clinching process works to create a joint
The clinching process joins two layers of sheet metal together with a mechanical interlock joint. The clinching tooling forces the sheet metal on the top layer, into the second layer, forming a permanent press fit. The steps of the clinching process are shown below in section view so that you can see the tooling itself. All of these steps happen within a second or less.
Two layers of sheet metal are inserted in the tooling.
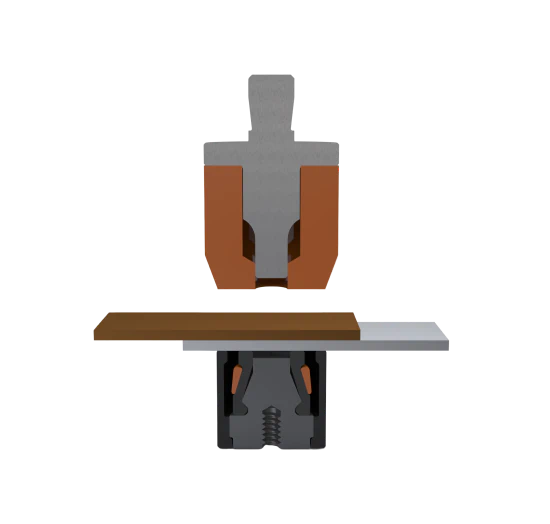
The punch descends, clamping the two layers of sheet metal between the punch and die.
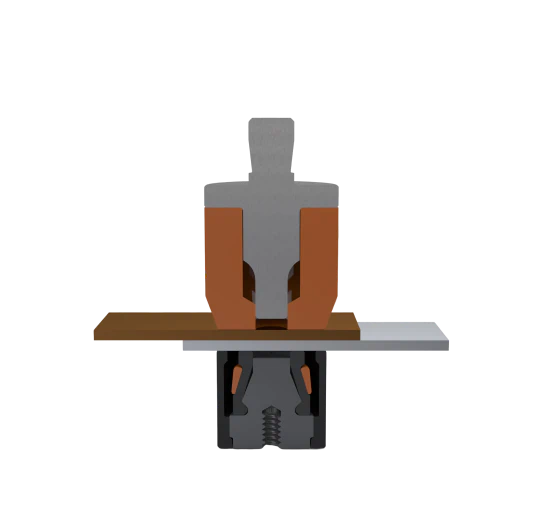
The punch advances and draws both layers of sheet metal down into the die.
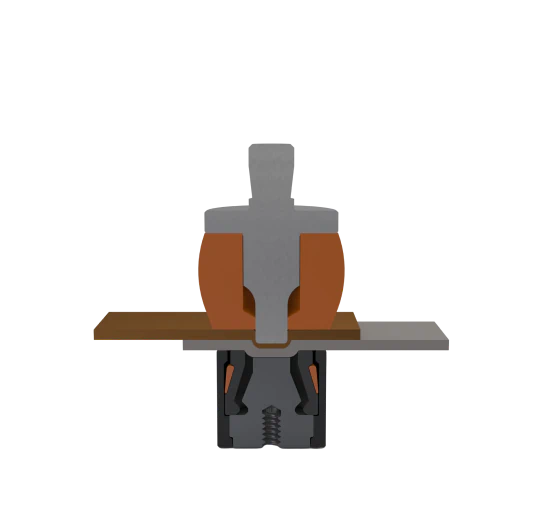
The punch squeezes the joint, forcing the top layer of sheet metal to flow into the bottom layer, forming the joint.
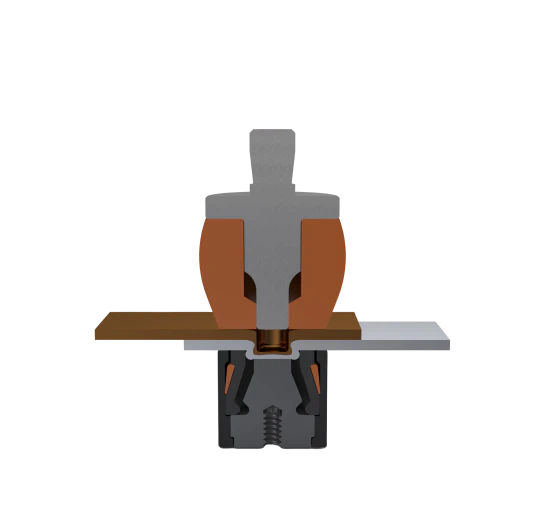
The punch retracts completely and the two layers of sheet metal are removed from the clinching machine.
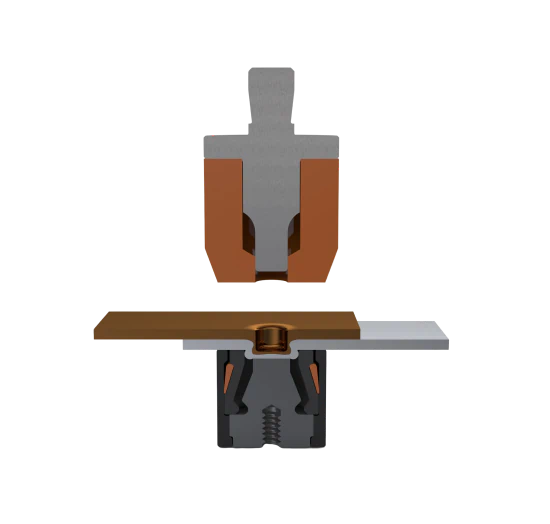
What are the advantages of clinching?
The advantages of clinching:
Green technology; no welding fumes
No heat affected zone
Low training requirements
Easily join un-weldable or dissimilar material
Easily join pre-coated material
Minimal maintenance
Portable and easily customized
High cycle speeds
Easily inspected via go/no-go gauging
What kind of tooling is required for clinching?
Here's a list of common parts and components used in metal clinching, specifically related to the punch and die assembly:
1. Punch: The tool used to create a hole or indentation in the metal sheets, initiating the clinching process.
2. Punch Stripper: This component helps remove the punched material from the punch and ensures smooth operation.
3. Die Anvil: Provides support to the metal sheets and helps distribute the force during clinching, serving as the counterpart to the punch.
4. Die Blades: These are the components within the die that come into contact with the punch and help shape the clinch joint.
5. Die Elastomer: Often made of rubber or a similar material, the elastomer returns the die blades to their home position after the clinch is formed. The strength and durability of this component is crucial to the clinching process.
6. Die Collar/Protector: the die collar forms the space the clinch is permitted to flow into while the joint is being squeezed. It also protects die blades from being pinched against material.
These parts are integral to the punch and die assembly, which is at the heart of the metal clinching process. The specific design and configuration of these components can vary based on the application and materials being joined.
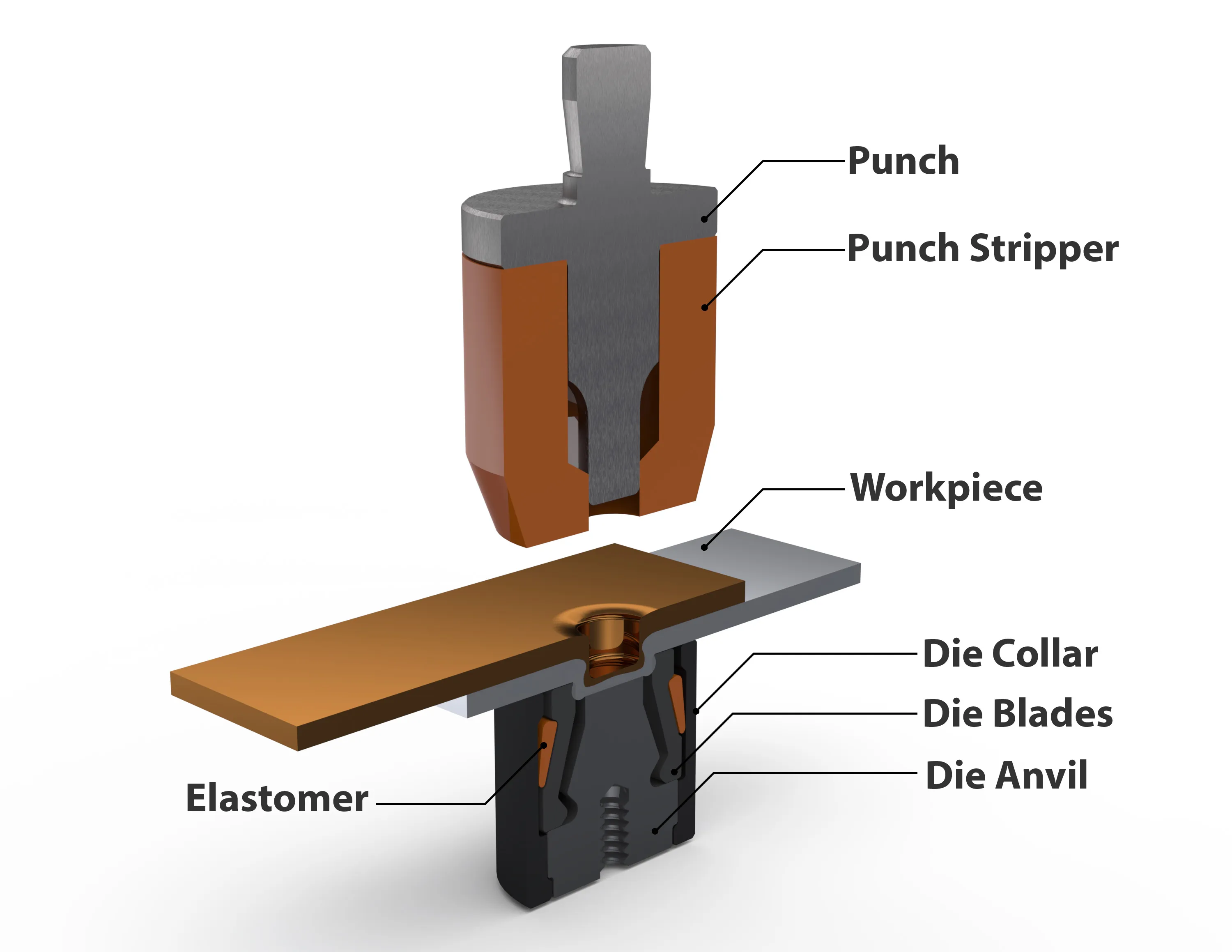
Clinching, welding, or riveting - which is right for your application?
Self-piercing rivets and clinching are non-thermal processes, meaning they do not generate heat during assembly. This eliminates the risk of warping or distortion in materials, making them ideal for joining material that is less than 0.25" (6.3mm) thick or sensitive metals.
Additionally, these methods are faster, requiring significantly less setup time than welding, which can boost production efficiency. Self-piercing rivets and clinching create joints without the need for consumable materials like welding wire or filler metals, resulting in cost savings. They also produce cleaner, more aesthetically pleasing seams, making them ideal for visible or finished surfaces.
It's important to note that welding still has its place in manufacturing. In scenarios where extremely high strength is required, or in applications involving thicker materials, welding may be the superior choice. Moreover, welding offers greater flexibility with a wider range of materials, and it's often the preferred method for critical structural components.
If you're not sure if your part can and should be clinched or riveted, reach out to our team or consider using our sample evaluation process.
Become a clinching expert with our guides & articles
Get up to speed on the latest metal industry trends, business tips and Press Lock Technologies product updates.
Frustrated by inconsistent material joining?
Download your 5 points cheat sheet and troubleshooting guide to improve your results today!