.webp)
There are many situations where using fasteners to join sheet metal just won’t work.
You might consider it for aesthetic reasons, such as a cleaner look. Or you might want a more even and uniform stress distribution to have extremely strong and durable joints. Fasteners can also create points where moisture and contaminants accumulate, leading to faster corrosion.
Here’s an overview of how to join sheet metal without using fasteners.
Ways to join sheet metal without fasteners
You can join sheet metal:
- Using a mechanical method, such as clinching or hemming.
- By welding the two pieces of metal together. There are various welding techniques, each with advantages and disadvantages, such as MIG, TIG, spot welding, or laser welding.
- Thermally using heat, such as brazing or soldering.
- By gluing them together using adhesives.
Clinching
Clinching involves deforming the materials being joined so that they interlock and form a strong, mechanical bond. It’s used in HVAC, metal buildings (roofing), elevator platforms, automotive, channel letter signs, and window frames.
Here’s a step-by-step outline of how clinching typically works:
- The metal sheets to be joined are positioned one on top of the other.
- A punch and die are used to apply localized pressure to the sheets. The punch pushes the metal into the die, creating a localized deformation.
- The lower sheet deforms to fit into a recess in the upper sheet, creating an interlocking mechanism that forms a button-like connection.
One of the things that makes clinching unique as a method is that you can use it to join multiple sheets of different metals, as well as metal with intermediate layers like damper material or seals.
But it’s important to note that a clinching joint is typically about 50% as strong as a joint that’s connected with spot welding. You need to be able to access both sides of the part and both the tonnage and the frame (the available material or distance to the edge) you need to go up as the punch tip diameter increases.
A good test to see if your metal can be clinched is to try to fold it into a seam without the corners cracking.
Hemming
Hemming involves folding the edge of a sheet over itself or another sheet to create a smooth, rounded edge that is both visually appealing and structurally reinforced. This method is commonly used in automotive and appliance manufacturing.
It often works best if you combine it with another joining method, like an adhesive.
Welding
Welding is a highly effective method for joining sheet metal, producing strong and durable joints. Welding processes involve melting the base materials to form a joint.
Common welding methods include MIG (Metal Inert Gas), TIG (Tungsten Inert Gas), spot welding, and laser welding and each of these methods have slightly different applications.
Welding produces extremely strong joints. When it’s done well, you can only take the joint apart by ripping the material itself, meaning the joint is often as strong as (if not even stronger) than the material you’re bonding. But clinching allows for a higher level of consistency in results because it doesn’t actually change the geometry of the piece you’re working with.
Brazing
Brazing uses a filler metal with a lower melting point than the base metals to create a strong, leak-proof joint. Brazing doesn’t produce joints that are strong as welded joints, but the lower melting point means that the risk of thermal distortion is lower as well.
Soldering
Soldering uses even lower temperatures than brazing and is typically used for joining thin materials and small joints, often in electronics.
The main difference between soldering and brazing is that soldering is a bit easier to automate for high-volume production. Otherwise, it can also be used to join dissimilar metals, and it’s a very low-temperature process–but it’s limited to thin materials and smaller joints.
Adhesives
Adhesives provide a versatile method for joining sheet metal. Adhesives create a chemical bond that glues the pieces of metal together. Adhesives are a great alternative to some of the stronger methods here. They distribute the load evenly across the joint, which can make extremely strong connections.
Exposure to heat and moisture can degrade the quality of the bond, though. And the surface preparation is critical for strong bonds, making adhesives even more time-consuming.
They can be an excellent partner with additional joining methods like clinching. Clinching allows you to process the metal much faster because clinch joints are enough to hold the pieces together, while the glue requires curing and drying time.
Choosing the right method for joining sheet metal
The primary factors that dictate which method you choose are:
- How strong the joint needs to be. Some joints carry critical infrastructure or are intended to secure people–where there’s a risk of fatal injury if the joint fails. Other joints are just holding material together for transport. In this case, the joint will never need to be stronger than the material itself.
- The geometry of the parts you’re joining. Different methods require a different level of access to the part. Can it be designed, so the machine can adequately access it and form a strong joint?
- The material you’re working with. As noted, some methods just won’t work for specific materials.
At Press Lock Technologies, we specialize in clinching (and self-piercing riveting, if you’re considering a method that does involve fasteners). We can help you identify the right clinching machine for your use case or advise you on available options.
If you'd like to discuss if clinching is the solution for you, don't hesitate to contact us today!
Take our 5-day course
Get an article every day for 5 days
Don’t have time to read everything now? Sign up and we’ll send you an article every day for 10 days.
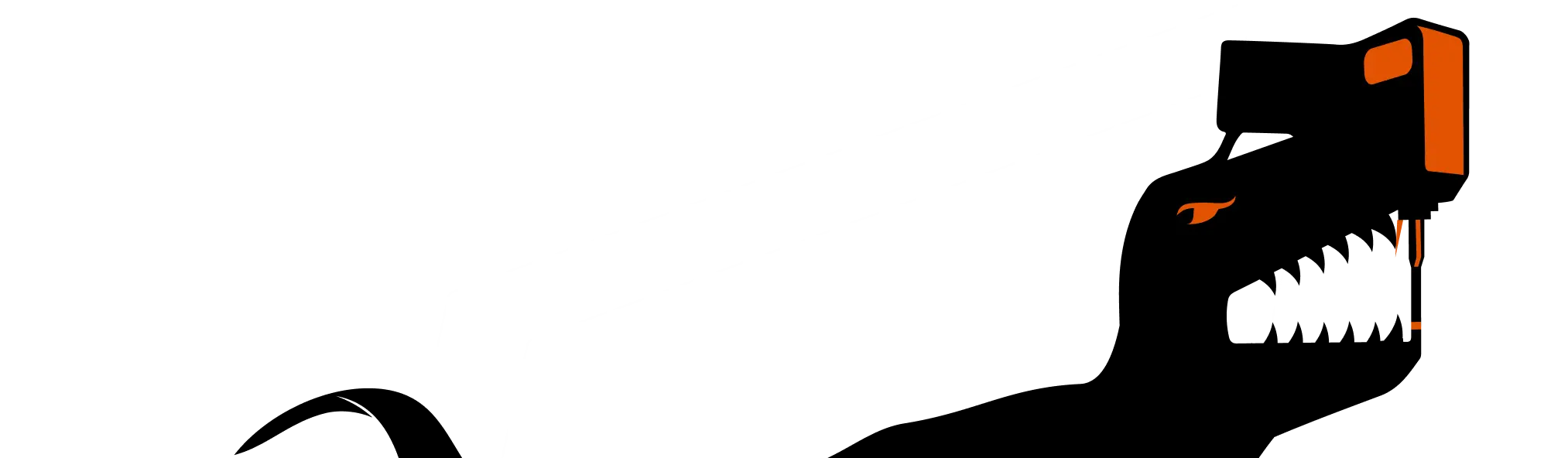